Brickmakers
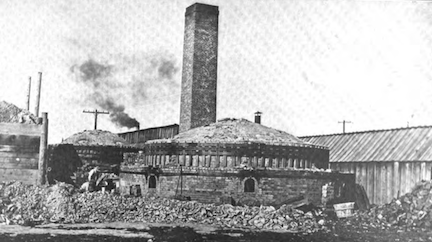
WASHINGTON BRICKS
Gladding, McBean and Company, Renton
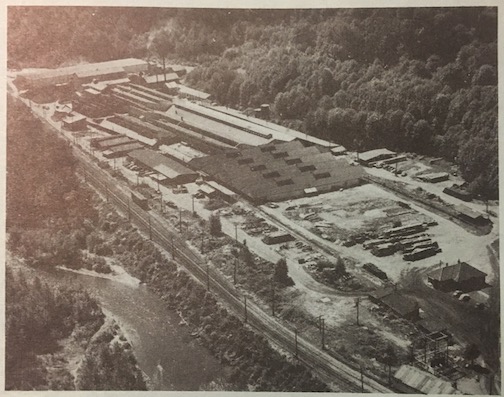
View of the Gladding, McBean and Company Renton plant. From Gladding, McBean and Company, 1951.
History
In 1927, Gladding, McBean & Company, a California-based company with headquarters at San Francisco, purchased the
Denny-Renton Clay & Coal Company and continued the manufacture of bricks at its Renton plant in King County, Washington.
The company officers for the Pacific Northwest region were Raymond Smith, vice-president; Willis E. Clark, supervisor of
factories; W. E. Lemley, general superintendent; and G. L. Rogers, chief engineer.
Eocene age Puget Group of shale and sandstone was mined at four locations. In the main quarry by the plant, 100 feet
of nearly horizontal laminated dark-gray and brown shales were worked between two massive sandstone strata. Dark brownish
gray clay was excellent for making paving and facing brick and hollow tile when fired to cone 06 to 02. The shale was
mined in tunnels run for 10 feet into the base of the quarry face. Each tunnel portal was protected by timbering 15 feet
out from the face over the track. The shale was blasted and caved down onto muck-boards above the tracks. The shale dropped
into waiting cars by lifting the muck-boards. Formerly there were 22 of these tunnels and tracks in the 750 feet of workings.
After 1936, a power shovel was used to load the cars. The cars ran 200 yards down by gravity to the tipple, where a gravity
car-dump emptied the shale onto a grizzly, which was at jaw-crusher that reduced the oversized shale. The crushed shale
was then conveyed by belt to a storage bunker. Other storage bunkers contained clays and shales from other mines and pits
owned by the company. In 1936, these storage bins had a total capacity of about 8,000 tons.
A quarry 420 feet long was worked at the Newcastle shale quarry, by the county road just outside of Newcastle. Here thin-bedded
unctuous shales, sandy shales, and a few sandstone layers were exposed. The shales were dark bluish gray and incline 35
degrees north. It was similar to the shale mined at Renton with a red-firing, low-fusing (cone 5) shale used for brick,
drain tile, and all red ware. It was mined by power shovel and taken to Renton by truck. At the Harris clay mine, 200 feet
south of the Superior coal mine of the Harris Coal Company, the company was mining a thick, hard claystone. The mine was a
750-foot long drift in the claystone and the clay was removed from rooms and pillars up dip (30-35 degrees) for 250 feet.
This clay was a very compact dark-gray to nearly black carbonaceous sandy clay with refractory properties used for making
No. 2 firebrick. The clay was taken by truck to the Renton plant. At the Issaqua clay pit, located a quarter mile west of
Issaqua, Gladding McBean mined a blanket of gray and stained plastic clay and sandy clay derived from weathered strata of
Eocene coal measures. This plastic clay was mined in a pit 100 by 125 feet. The clay was light firing and fused at cone 15.
It was used as a bond and tightener in some refractory bodies. It was taken to the Renton plant by truck.
The plant was located one-half mile east of Renton on the south side of the Cedar River Valley. From the storage bins,
underground conveyor belts transported the crushed shale to one of six 9-foot dry pans for further grinding. The grounded
clay was then elevated, screened, and dropped into the ground-clay storage bunkers. In 1936, about 150 tons of raw clay
was used daily. It was from these storage bunkers that clays were taken in certain proportions to be sent to three lines
of pug mills and auger machines. In two of the lines, the clay was vacuum deaired for making paving brick and all structural
materials. The third and larger line was used for all refractories. The plant also had one 4-brick dry-press machine and
facilities for hand-molding of special firebrick shapes.
The bricks were placed on cars to be sent to two types of driers. One was an 8-track carrier drier of 120-car capacity
that was heated by waste heat and steam. The second a 28-tunnel double track drier, with 30 cars to the tunnel, and heated
by an auxiliary furnace.
A Harrop tunnel kiln was used for firing the refractory ware and also for buff face brick and glazed wall block. This kiln
was 319.5 feet long and had a capacity of 52 cars, each car holding 1,200 firebrick or their equivalent. The cars took 104
hours to pass through the kiln. The hot zone, fired by six oil-burners on each side, reached a temperature of cone 13 in
1936, and was later to be increased to cone 16. Five rectangular periodic down-draft kilns, 16 feet wide and 70 to 150 feet
in length, and four 30- to 34-foot diameter found down-draft kilns were used to fire all red-firing ware and some of the
buff face brick. Temperatures in these kilns were measured using by thermocouple pyrometers and checked by optical
pyrometers and cones.
This plant was a major producer of refractory products for Gladding McBean, forming 75 percent of the output. The brands for
firebrick made at this plant in 1951 include its super duty OLYMPIC dry press, high duty COLUMBIA-X dry press, intermediate
duty COLUMBIA JR. dry press, CASCADE dry press, and low duty FIRE BACK dry press. Earlier firebrick brand from the 1930s
include PACIFIC. They also sold plastic firebrick in 100 pound cartons, and castable refractories, ground fireclay, and
mortar in 75- and 100-pound bags. Other products in decreasing order of output tonnage included paving brick, acid brick,
blowpit brick, face brick, roofing tile, glazed wall block, quarry tile, and architectural terra cotta. These products
supplied the Pacific Northwest territory of Gladding, McBean and Company.
In 1962, Gladding, McBean and Company merged with the Lock Joint Pipe Company in New Jersey to form the International Pipe
and Ceramics (Interpace) Corporation of New Jersey. Interpace continued to operate the Renton plant for two decades.
Gladding McBean Bricks Made at Renton
Firebricks
Fireback
Fireback is a low-duty firebrick. The color is uniform yellowish buff. Form is excellent with straight sharp edges and sharp
corners, if not broken. Surface is smooth with visible tiny round brown iron oxides. The marked face displays the oval logo of
Gladding McBean, 2 by 1 1/2 inches, over the brand name FIREBACK in recessed block letters inside a tight rectangular name plate.
The brand name spans 4 5/8 inches and stands 3/4 inch tall. Interior is composed of fine granular cream alumina clay with 10 percent
subangular clear quartz, 1/32 inch in diameter, and 15 percent round brown iron oxides, as much as 1/4 inch in diameter,
some with blister holes. This brick was made using the dry press process. Length 9, width 4 1/2, height 2 1/2 inches.
![Marked face of the [GMcB oval logo] / FIREBACK brick](brick.gmbfireback.jpg)
View of the marked face of the Fireback firebrick. Photo courtesy of George L. Kennedy.
![Side of the [GMcB oval logo] / FIREBACK brick](brick.gmbfireback2.jpg)
View of the side of the Fireback firebrick.
![Unmarked face of the [GMcB oval logo] / FIREBACK brick](brick.gmbfireback3.jpg)
View of the unmarked face of the Fireback firebrick.
![End of the [GMcB oval logo] / FIREBACK brick](brick.gmbfireback4.jpg)
View of the end of the Fireback firebrick.
![Interior of the [GMcB oval logo] / FIREBACK brick](brick.gmbfireback5.jpg)
View of the interior of the Fireback firebrick showing fine
grained cream alumina clay, white quartz, and brown iron oxides.
![Microscopic view of the interior of the [GMcB oval logo] / FIREBACK brick](brick.gmbfireback6.jpg)
Microscopic view of the interior of the Fireback firebrick
(50x, field of view is 1/4 inch).
Columbia
Columbia is an intermediate-duty firebrick. This may be the same as what Gladding McBean called "Columbia Jr" brand in its
catalog. The color is uniform buff. Form is excellent with straight sharp edges and sharp
corners, if not broken. Surface is smooth and displays some crackling. Flattened grains on the surface indicates a dry-pressed
brick. The marked face displays the brand name COLUMBIA over the oval GMcB logo centered on the face. The brand name is
recessed in block letters. This brick was made using the dry-pressed process. No dimensions available.
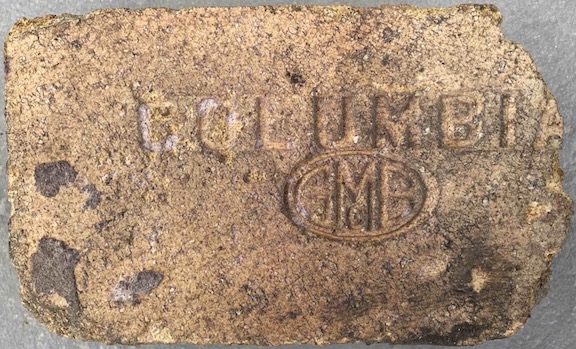
View of the marked face of the Columbia firebrick.
Columbia 2
Columbia 2 is an intermediate-duty firebrick. The color is uniform buff. Form is excellent with straight sharp edges and sharp
corners, if not broken. Surface is smooth and displays some crackling. The marked face displays the brand name COLUMBIA 2 over
the company name GLADDING McBEAN & CO. in recessed block letters. The letters are truncated at the edges by the rotating
name stamp and parts of the name are repeated. This brick was made using the stiff-mud process. No dimensions available.
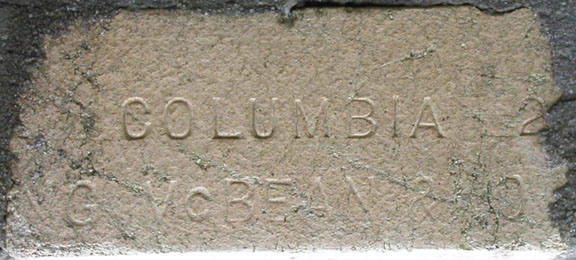
View of the marked face of the Columbia 2 firebrick.
Columbia-X
Columbia-X is an high-duty firebrick. The color is uniform buff. Form is excellent with straight sharp edges and sharp
corners, if not broken. Surface is smooth and displays round black iron oxides and white quartz. The marked face displays
the brand name COLUMBIA-X in recessed block letters inside a rounded rectangular name plate. This brick was made using the
dry press process. No dimensions available.
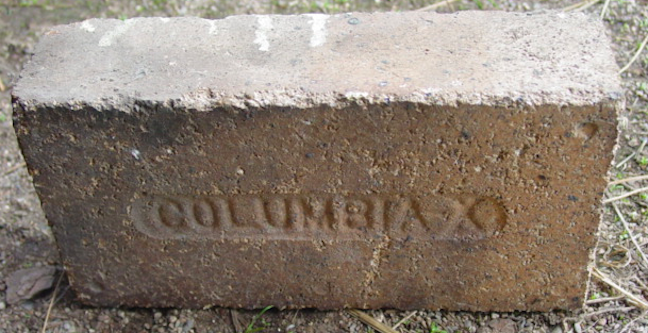
View of the marked face of the Columbia-X firebrick. Photo courtesy of Mike McWatters.
Pacific
Pacific is a buff firebrick with uniform color. Form is excellent with straight sharp edges and sharp
corners, if not broken. Surface is smooth and displays visible clasts of white quartz. The marked face displays the oval logo
of Gladding McBean over the brand name PACIFIC inside a tight rectangular name plate. This brick was made using the dry press
process. No dimensions are available.
![Marked face of the [GMcB oval logo] / PACIFIC brick](brick.gmbpacific.jpg)
View of the marked face of the Pacific firebrick. Collection of Sam Burton. Photo courtesy of George L. Kennedy.
Pacific 8
Pacific 8 is a buff firebrick with uniform color. Form is excellent with straight sharp edges and sharp
corners, if not broken. Surface is smooth and displays crackling. The marked face displays the brand name 8 PACIFIC
over McBEAN & CO GLADDING recessed in block letters 3/4 inch tall. The letters are truncated at the edges by the
rotating name stamp and parts of the name are repeated. This brick was made using the stiff-mud process. The large
size indicates that this is a block. Dimensions are length 13 1/2, width 3 3/4, height 4 inches.

View of the marked face of the Pacific 8 firebrick.
Olympic
Olympic is a super duty buff firebrick. Form is excellent with straight sharp edges and sharp corners, if not broken.
Surface is smooth. White quartz grog and brown to black iron oxide are visible on the surface. The face is marked with
the brand name "OLYMPIC" in block letters inside a rounded rectangular name plate. Interior is composed of 25 percent
white subangular white quartz and black iron oxide, all less than 1/4 inch across, in a compact clay body. This brick
was made using the dry press process. No dimensions available.
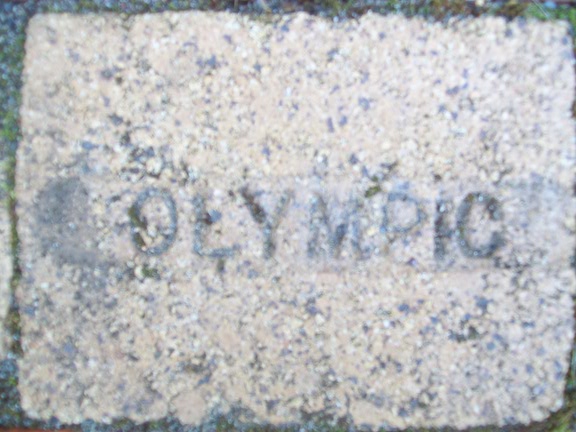
Photo courtesy of Dave Garcia
References
Garcia, Dave, written communication, 2019.
Gladding, McBean and Company, Refractories Handbook, 1951.
Glover, Sheldon L., Clays and Shales of Washington, Washington Division of Geology Bulletin 24, 1941.
Gurcke, Karl, Bricks and Brickmaking, University of Idaho Press, Moscow, Idaho, 1987.
Gurcke, Karl, written communication, 2017.
Hilding, Tina, Renton history built with bricks, Black Diamond History, accessed 3 November 2017,
https://blackdiamondhistory.wordpress.com/2017/08/26/renton-history-built-with-bricks/.
Install 325 Ft. Kiln at Renton, Wash., Plant, Brick and Clay Record, v. 85, no. 6, 1934, p. 185.
Kennedy, George L., written communications, 2017.
Matsumura, JoAnn, written communications, 2017.
McWatters, Mike, written communications, 2017.
Copyright © 2017 Dan Mosier